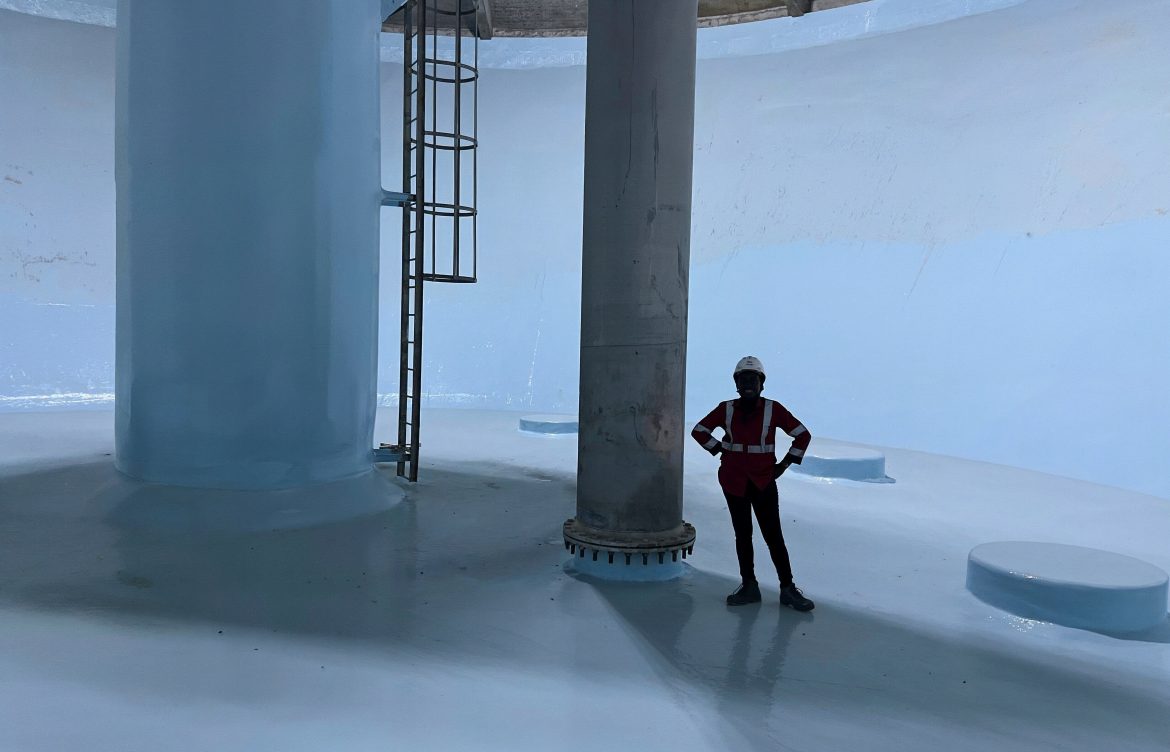
Cistern Liner Coatings and the Problem Beneath the Surface
Why Tank Movement Changes the Story After Spraying
Most polyurea applications for cistern liner systems begin with a solid surface and a quick timeline. Spray it fast, let it cure, and move on. The liner forms a watertight seal that holds against pressure and protects from corrosion. But what rarely gets discussed is how the tank behaves after the coating sets. A concrete cistern, especially one built below grade, doesn’t remain still. It breathes with temperature changes. It settles with time. It absorbs and releases moisture through pores that never quite stop moving. That slow shift beneath the surface determines whether the polyurea will last—or pull apart one inch at a time.
Where Polyurea Performs Best—and Where It Needs Help
A sprayed polyurea cistern liner performs best when applied to a clean, stable surface. Polyurea forms a monolithic membrane that flexes with the tank and shrugs off water. But that same strength can work against itself when applied over a wall that begins to move differently than expected. The liner bonds with force. And once it grips, it holds—even if the wall behind it begins to pull in a different direction. That grip, though strong, becomes the point of stress when pressure builds from behind. If the tank wall shrinks slightly due to cooling or shifts from soil movement, the liner doesn’t know how to follow.
How Corners Become the Weakest Link
Inside a cistern, the spot where the wall meets the floor carries more stress than any other. That curve—or hard corner, in some designs—acts like a hinge when the tank expands and contracts. If the polyurea isn’t layered thick enough in that area, or if it stretches too far during curing, the tension pulls at the surface like a paper seam. This is where failure usually begins. It doesn’t come from poor spraying. It comes from ignoring the mechanical behavior of the tank after the job is done. As cistern coating methods improve, installers must pay more attention to these points of tension, not just to the open areas that are easy to spray.
Tank Purpose Should Shape the Liner Method
Some tanks hold drinking water. Others manage irrigation water, runoff, or industrial reuse. Each purpose changes how the tank behaves. Tanks used for potable water storage require food grade coatings that resist chlorine or disinfection byproducts. But that’s only part of the story. A tank that fills once a week handles pressure differently than one that fills and drains several times a day. That variation affects how the liner wears at seams, anchors, and penetrations. The liner material must match both the contents and the usage pattern—not just the chemical profile.
Custom Fit Makes the Difference in Movement Control
A sprayed liner can’t always rely on thickness alone. Custom cistern liners built for water storage tanks with complex geometries need reinforcement in areas where movement concentrates. Matching the liner to the exact dimensions of the tank helps prevent rippling or stress fractures. It also helps avoid material waste and minimizes overspray in areas that don’t require it. That kind of design-based application—rooted in how the tank behaves over time—helps extend the lifespan of the liner by reducing the points where failure tends to begin.
What Experts Don’t Say Loud Enough
Discussions about what are cistern liners often start and end with technical specs: tensile strength, elongation, cure time, and adhesion. These all matter. But they don’t reflect the experience of tanks installed decades ago, where uneven settling or patchwork repairs create irregular behavior under load. Spray-applied polyurea has the tools to handle this environment—but only when used with knowledge of how the tank will change after the job ends. Polyurea doesn’t fail from water. It fails from tension that goes unnoticed.
Conclusion
Polyurea cistern liner coatings work—when applied with attention to more than pressure and cure time. The tank itself, not the sprayer, sets the conditions for success. A tank that moves will always test the liner’s ability to follow. That’s why the best liners don’t just seal the surface. They absorb its change. They allow the structure to breathe without breaking. In that quiet flexibility, real protection forms. Not because the product is strong, but because it was placed with care—on a surface someone took the time to understand.