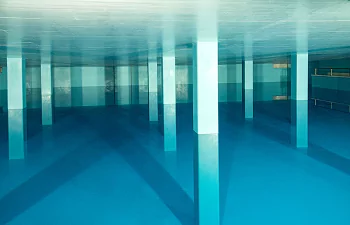
Rating the Top 5 Cistern Coatings
What Performance Really Means in Cistern Protection
Every coating promises protection, but not all coatings hold up the same way once water, temperature, and structural movement come into play. A cistern doesn’t just hold liquid—it breathes, shifts, and settles over time. Inside that environment, the coating doesn’t just stick to the wall. It responds to it. Judging which coatings perform best involves looking past technical claims and focusing on how each material works within the tank’s long-term conditions.
Polyurea: When Flexibility and Bond Strength Combine
Polyurea performs under pressure in ways most coatings don’t. It applies quickly, cures within seconds, and forms a seamless barrier that moves with the structure rather than fighting against it. That flexibility matters when cistern walls expand during warm weather or absorb moisture through porous surfaces. In real-world settings, polyurea continues to outperform because it doesn’t rely on the substrate remaining perfectly still. Even after years of service, polyurea liners show fewer signs of peeling or seam wear. Their success depends not just on application skill but also on how well the coating tolerates change.
Epoxy: A Durable Option with Limits
Epoxy coatings remain a common choice for cisterns, particularly where budget or tradition drives selection. When applied correctly, epoxy creates a rigid, chemically resistant surface that holds up under moderate use. The challenge comes when the tank sees frequent load shifts or sits outdoors where seasonal expansion and contraction occur. Epoxies tend to separate at corners and penetrations when the surface moves. In controlled indoor systems, they work well. But for older cisterns—especially ones made of concrete—the rigid bond struggles when surface stress increases over time.
Cementitious Liners: Strong Bond, Slow Failure
Cement-based coatings appear solid and durable when first applied, especially inside cistern liner systems that need to follow rough or irregular surfaces. They integrate well with concrete walls and can fill gaps or patch erosion. The drawback appears months or years later when tiny cracks begin to form. These cracks follow the same lines as the substrate, meaning any pre-existing weakness transfers directly through the coating. Once these lines open up, the coating loses its seal, and the repair process often requires full replacement rather than simple patching.
Urethane: Flexible But Often Thin
Urethane coatings deliver a soft, adaptable layer that conforms to the shape of the cistern without adding much bulk. Their chemical resistance makes them a good fit for tanks that store treated water or alternative liquids. But urethane often lacks the thickness and elongation strength needed for long-term performance under hydrostatic load. In deep cisterns, the pressure along the bottom can push urethane coatings past their limit. While newer formulas improve durability, the trade-off remains between ease of application and long-term sealing strength.
Rubberized Coatings: A Temporary Fix in Many Tanks
Rubber-based liners and coatings offer quick relief for leaking or aging tanks, especially when applied over flexible surfaces or plastic cisterns. Their adhesion tends to fall short on concrete or masonry surfaces unless extreme surface prep is completed. While the coating stretches, its bond weakens over time, particularly around outlets or corners. In emergency situations, rubber works well as a short-term barrier. But in most cistern systems, long-term use reveals patch failures and areas where bond loss causes bubbling or liner lift.
Final Observations: Where Coatings Prove Themselves
No coating works the same in every cistern. The right choice depends on wall condition, expected movement, water chemistry, and the shape of the tank itself. That said, polyurea continues to rank highest for systems where both flexibility and permanence matter. It doesn’t rely on a motionless tank. It becomes part of the surface and adjusts as conditions shift. When paired with solid design and prep work, polyurea coatings carry the kind of confidence that doesn’t need claims. It holds, year after year, because it was built to work where tanks live—in the ground, in motion, and under pressure.