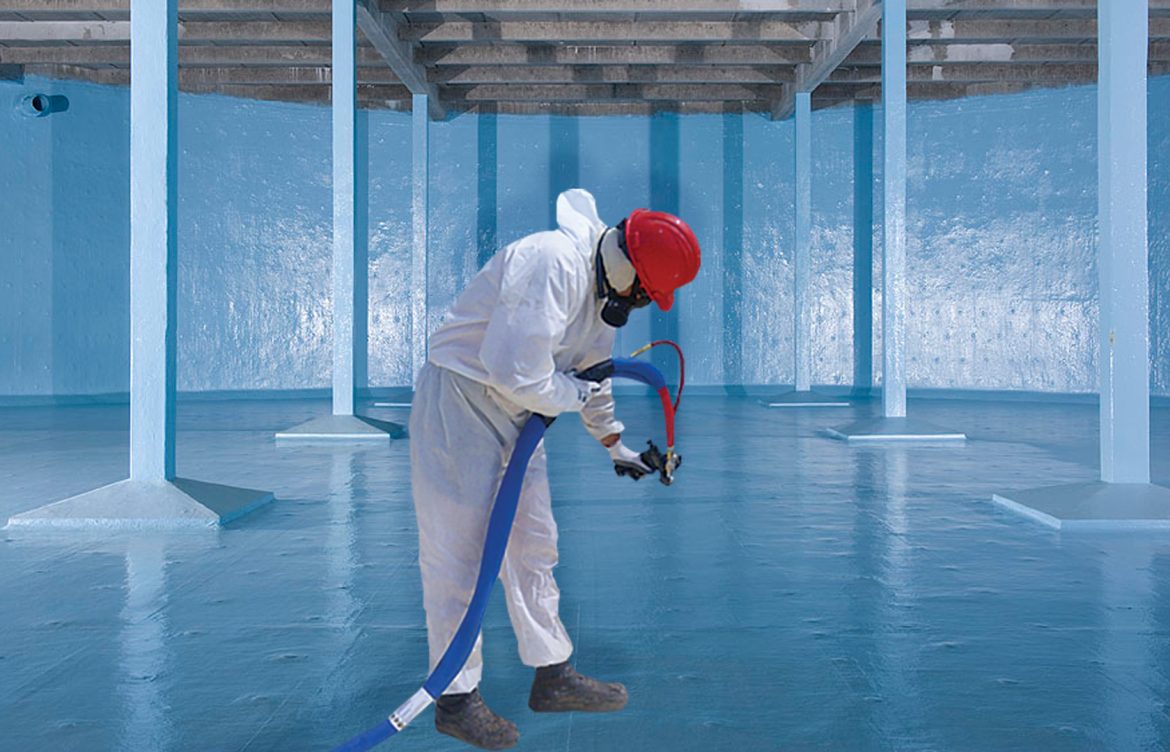
Understanding Cistern Liner Coatings: What Works, What Fails, and Why Design Matters
Where Most Cistern Liners Begin to Fail
A cistern serves a clear purpose: hold water, protect it from contamination, and retain structural integrity for decades. But inside the tank, the conditions aren’t always as stable as they seem. Moisture builds behind walls, temperature shifts stress materials, and movement—small but constant—alters the shape of the surface just enough to affect the coating. Many failures in cistern coating systems don’t begin with product choice. They start where the tank changes and the coating doesn’t. This is especially true in old concrete installations, where surface irregularities, repairs, and corner transitions put more stress on the liner than any chemical it holds back.
Why Polyurea Changes the Game
Spray-applied polyurea offers a different kind of performance. It stretches where rigid materials crack. It bonds fast and resists chemical breakdown. More importantly, it conforms to tank geometry in ways older coating types cannot. In a polyurea cistern, the liner becomes a monolithic layer—no seams, no gaps, no overlaps—just continuous coverage. That single-skin approach solves the problem of adhesion at critical angles, like where vertical walls meet floors. But even polyurea relies on one condition for success: movement must be anticipated. The tank’s behavior, not just its surface, determines the outcome.
The Role of Design in Liner Longevity
Most tanks don’t crack open. They fail slowly—at the seams, the penetrations, and the points of uneven thickness. The cistern liner design must reflect how water behaves inside the tank and how the tank behaves under pressure, empty or full. It must account for past repairs and variations in construction. A well-designed polyurea coating allows for minor expansion and contraction without delamination. A poor design, no matter how well applied, creates stress concentrations that eventually lift the coating from the wall. The best cistern liner systems begin with observation—not spraying.
What Material Specs Don’t Tell You
It’s easy to compare liners by cure time or tensile strength. What those numbers don’t reveal is how a coating handles after years of shifting humidity, sediment buildup, and minor structural shifts. The material factor in cistern liners becomes most obvious not on day one but year five, when coatings either hold or separate at the anchor points. Polyurea performs well in these areas because it doesn’t harden in a way that resists the tank—it moves with it. It adapts, holds, and resists intrusion from the outside, even after years of loading and unloading cycles.
How Application Matches to Use Case
Every tank stores something slightly different—drinking water, rainwater, irrigation reserves, or treated runoff. The cistern liner types vary with these uses, as do the liner thickness, curing method, and anchoring approach. Some tanks need coatings that comply with potable standards. Others require coatings that resist constant abrasion or frequent chemical exposure. The key is matching coating characteristics with storage behavior—not just volume. Liner failure often happens not because of the wrong product, but because the installer didn’t account for how the tank gets used.
Understanding What a Cistern Liner Really Is
At its core, a cistern liner is a barrier. But more than that, it becomes part of the tank’s internal structure. A liner that works must disappear into the background. It must do its job without drawing attention. That means handling vibration, seasonal shifts, and structural fatigue without cracking or peeling. Answering the question of what are cistern liners requires more than chemistry—it requires understanding tanks as living systems. They shift. They breathe. They require coatings that do the same.
Conclusion
Choosing a cistern coating doesn’t begin with a product. It begins with understanding the tank—its surface, its history, and its future use. Spray-applied polyurea continues to outperform many traditional liners, not because it is stronger, but because it adapts better. A successful cistern liner project relies on cistern liner design, site knowledge, and long-term thinking. Inside that process, the right coating becomes not just a layer—but a solution that holds through the unseen strain every tank endures.